An aluminium window comprises sophisticated aluminium extrusions, designed and produced to strict quality and industry standards.
Of course, aluminium can be coloured, but the choice of colours, textures and finishes available does need explaining. In the article, we explain the various methods that apply when painting and protecting aluminium extrusions, windows and doors.
Why does aluminium need to be painted?
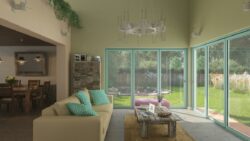
The main reason why aluminium needs to be painted or finished is to provide protection.
When an aluminium extrusion is created and extruded, it is in its raw form. This is referred to as Mill Finish.
Mill finish aluminium extrusions are untreated. When these are exposed to external elements, a chemical reaction will take place. Oxidisation occurs whereby an oxide layer forms on the surface of the profile. Over time, this oxide becomes thicker and more prominent.
Can you make a window or a door in mill finish? Yes, you can, but the entire surface of the aluminium is exposed and unprotected.
Therefore to provide protection and durability to a powder coated aluminium window, the various processes available to colour and protect aluminium are used.
How is colour chosen for aluminium windows and doors?
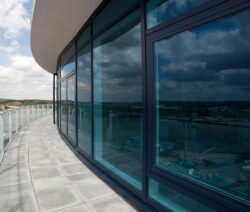
Residentially, simple tastes, trends and personal choice are the three factors that determine the choice of colour.
Architects, however, look at the colour choice somewhat differently. For a building designer, it is not just about the colour of the windows or the doors but three other common factors. These are:
- The desired appearance of the finished building.
- The colour appearance desired such as matt, satin, gloss, metallic or textured.
- The level of protection the aluminium painted material requires.
Four finishing methods are available for aluminium.
Anodising.
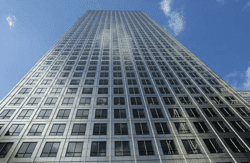
Anodising is one of the first processes used to finish aluminium as early as the 1930’s. Anodising provides a superb looking finish to an aluminium window, offers excellent protection and looks very impressive.
Anodised aluminium is the one finishing process to replicate the original metal appearance of untreated aluminium virtually. Other shades are available.
Anodising came about long before the more popular powder coating process. It is rare for residential systems to be offered as an anodised product mainly because many installers consider it too difficult to procure. This is not the case, and there are enormous advantages provided by anodised aluminium.
Features of Anodised Finishes:
- Does not come in the colour choices offered by powder coating.
- Very popular with architects.
- Offers high protection and a contemporary metal aesthetic.
- Anodised finishes will not provide colour consistency
- Anodising is hard to repair.
- Anodising is unsuitable for welded aluminium.
Polyester powder coating.
Powder coating is a paint finish that is very familiar to most people. It offers a very wide colour range with over 200 different colours possible.
Powder coated colours come in six references and standards. These are:
- RAL
- Syntha Pulvin
- BS 4800
- BS 381C
- NCS
- Pantone.
The above references all provide the same shade of colour, although differences can apply. This is because these references relate to powders all made by different powder manufacturers.
PVDF Finishing.
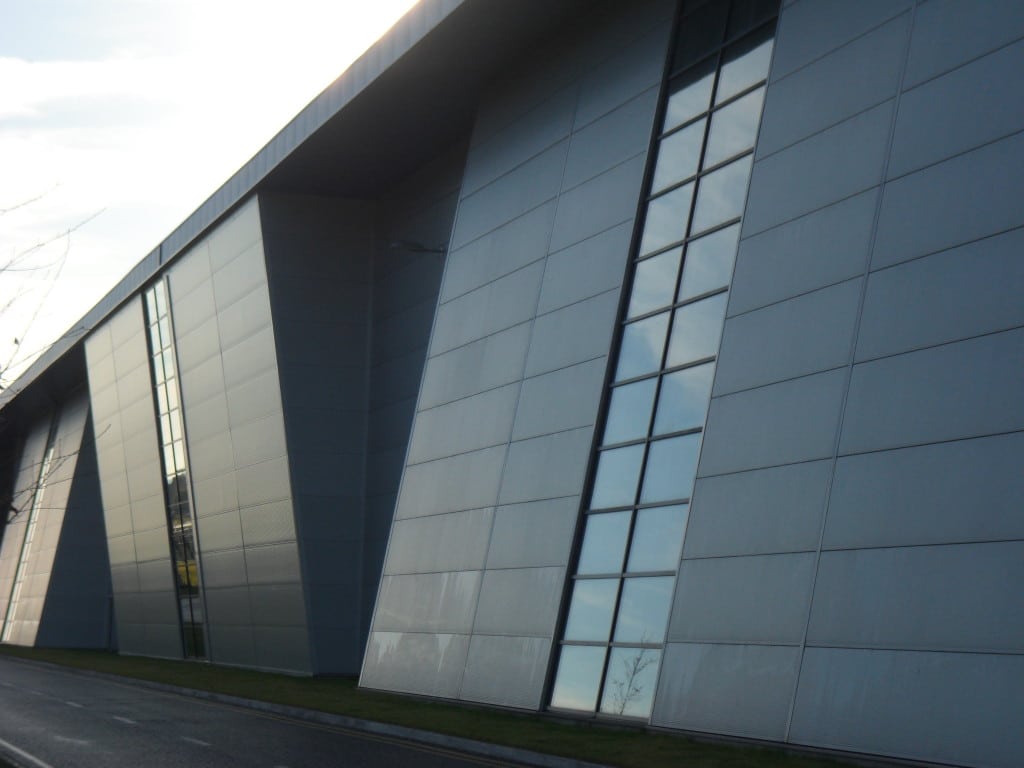
PVDF treatments use a combination of chemicals. These are Polyvinylidene Fluoride and an acrylic resin. Polyvinylidene Fluoride is the greater quantity of compared to acrylic. Unlike powder coating that is a dry powder process, PVDF is a wet paint process.
Powder coating and anodising are cheaper than PVDF. However, PVDF offers better protection to an aluminium surface.
Features of PVDF Coatings:
- Not as scratch resistant as powder coated or anodised treatments.
- PVDF provides exceptional resistance to sunlight.
- PVDF is chosen over powder coating for aluminium panels, pressings and cladding.
- Countries such as the Middle East with very intense sun and high heat prefer PVDF to powder coating for its fade and chalking resistance.
Sublimation.
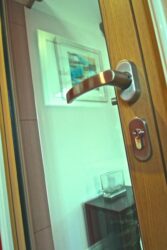
If you have ever seen wood effect aluminium doors and windows, these are coloured with a process called sublimation.
Sublimation the transfer of dyes onto the aluminium surface to create the effect of wood, stone, marble or virtually any other design. Sublimation is widely used on other aluminium consumer products such as kitchens, benches, aluminium household goods and many others.
The aluminium extrusion is powder coated with a base coat and then wrapped in a bag containing the wood or other effect design. The air is withdrawn to create an airtight seal so that the pattern makes contact with the aluminium. The extrusion is baked at approximately 200 degrees and the wood effect transfers onto the aluminium.
The effect is a very authentic appearance on an aluminium product that is very durable, can be repaired and offer a very long service life.
Other methods that aluminium can be coloured and finished.
There are other methods used to colour aluminium that involve wet spraying or electrophoretic finishing. However, these are rarely used in the ‘architectural aluminium’ application that is windows and doors.